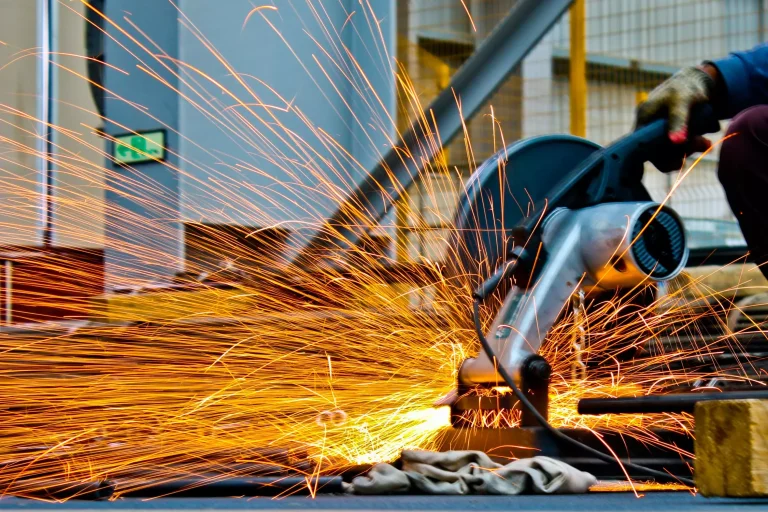
Heavy machinery operation and moving parts can cause death or serious injuries such as crushed limbs and amputations. According to the Workplace Safety and Health Council (WSH), two (2) workers die and 1,000 workers are injured while working with machines yearly. Therefore, risk assessments must be carried out, and safety protocols are abided by to ensure worksite safety. Here are eight (8) ways to improve construction site safety:
1. Maintain a safe distance from heavy machinery
Heavy machinery has many moving parts that may move in a linear, reciprocating, rotary, or oscillating motion, individually or in combination. In many cases, the action of these moving parts can exert sufficient force to cause injury to workers operating the machine. WSH cites that heavy machinery poses various safety breaches such as crushing hazards, impact hazards, and shearing hazards. Such risks occur when workers are working within the impact zone where any accidents happen. Workers should stand clear of machinery when it is in use.
2. Proper usage of Personal Protective Equipment (PPE) such as Helmets, Vests, Boots, and Gloves
To prevent workers from sustaining injuries when using heavy machinery, personal protective equipment (PPE) should be worn at all times. Hard hats protect from injuries such as penetration, electric, and substantial head impacts, which can be caused by flying or falling objects. Proper gloves and goggles should be used when dealing with machinery with moving cutting elements that may cause lacerations. Safety officers should also enforce the appropriate and adequate usage of safety vests, as loose clothing or straps may get caught between the moving parts of the machinery leading to an entanglement injury.
3. Implement preventive measures for construction site safety
According to WSH standards, machine guards can be fitted onto the piece of machinery to prevent accidents. Machine guards are rigid physical barriers that enclose dangerous machine parts and restrict operator access to hazardous areas. Machine guards often partially cover the point of operation while allowing limited or no access. Presence-sensors can also be adopted in danger zones. These sensors will immediately cease machine operations when a presence is sensed in the danger zone. Safety mats can also be employed. Pressure-sensitive safety mats protect workers around hazardous machines by sending a signal to stop the engine when the machine operator steps onto the carpet. This preventive safety equipment can be utilized in tandem with dangerous machinery to alleviate risks.
4. Adequate training in machinery usage
Workers who operate machines must be trained, competent, and suitably supervised not to endanger themselves and others at work. Proper machinery usage is essential so that workers are apparent in the procedures and do not engage in unnecessary or wrong actions that may expose them to machine hazards. According to WSH, machine operators must ensure that the engineering control measures are in place, adhere to safe work procedures (SWPs) and use appropriate PPE. Companies should also provide training for new and existing operators at regular intervals. Similarly, when new machines are introduced or when modifications are made to existing devices, training should be administered. Operators should also always be up to date with any changes to the SWPs. All these efforts add up to construction site safety.
5. Proper shift management
Fatigue is a state of tiredness leading to reduced mental and physical performance that can endanger workplace safety and workplace health. Workers must be in good condition during work as a lapse in judgment and concentration can result in severe consequences. Managers can prevent this with proper schedule management. Complex tasks should be scheduled only during the day, and schedules should be planned and communicated to the workers clearly. Safety officers should also ensure sufficient recovery time between shifts and encourage workers to take scheduled breaks to relieve fatigue. These measures can ensure that workers are in good mental and physical condition leading to a safer workforce.
6. Routine checks and maintenance of machines and equipment
A thorough and effective maintenance program should be established for all machines and equipment used. This will help prevent accidents from happening due to machine or equipment failure. Heavy machinery is full of moving parts that will eventually cause wear and tear, posing a safety risk. This can be resolved with proper checks and regular maintenance. A program with inspection and maintenance schedules and wherein records for each machine and a system for workers to report any defects or damages should be implemented. Regular lubrication of moving parts is also necessary to ensure that the equipment works as it should.
7. Adopting safer machine designs
Machinery and equipment with inherently safe machine design can be adapted for use. This can be done by designing machines with accessible parts without sharp edges, sharp angles, rough surfaces, or any protruding parts likely to cause injury. Openings that can trap parts of the body or clothing can also be removed. The gap between moving parts can also be increased such that the parts of the body, e.g., one’s fingers, can safely move through the opening or reduce the gap so that no part of the body can enter it. Machinery and equipment used at a worksite should comprise components that are well made and are of good quality. This would enable the equipment to be used over more extended periods and increase the reliability of these machines reducing workers’ exposure to hazards.
8. Consider AI construction technology to improve construction site safety
Man-machine interaction is one of the biggest reasons behind accidents involving heavy machinery. Reducing the interactions required will help to minimize the number of incidents. This can be implemented through the integration of automation. The usage of industrial robots is one such example, where the need for physical operators is not needed, reducing the chances of worksite accidents occurring. Other automation measures include automatic handling devices and transfer mechanisms that would allow such systems to be operated at centralized locations, a safe distance away from the machinery at work. Artificial intelligence-powered cameras such as Safekey can be used to alert safety officers when workers enter the marked-out danger zones. They will also be helpful in identifying the wrong usage or absence of PPE, detection of lack of barriers and guardrails, and other use cases. AI systems can also be integrated with heavy machinery. Through predictive analysis, these systems can predict when machines require maintenance and even predict any mishaps that may occur.
Video analytics can save lives in the workplace and improve the workplace safety culture. Follow our website and updates for more information, and sign up now for a free and customized demo. We can show you how your cameras can be converted into smart 24/7 safety enforcers and upgrade your worksite.
2 Comments
[…] severe consequences such as crushed limbs and amputations. There are several ways to cautiously operate heavy machinery and equipment in a construction site to reduce workplace […]
[…] safety hazards are slip and trip falls, heavy machinery, and hazardous materials. Exposure to such hazards can lead to accidents if no proper safety […]